آمونیاک چیست و چه کاربردهایی در صنایع مختلف دارد؟
آمونیاک ترکیبی شیمیایی با فرمول NH₃ گازی بی رنگ با بوی تند و زننده است که نقشی حیاتی در صنایع گوناگون ایفا می کند. این ترکیب شیمیایی که از یک اتم نیتروژن و سه اتم هیدروژن تشکیل شده است به دلیل خواص منحصر به فرد خود کاربردهای گسترده ای از تولید کودهای کشاورزی گرفته تا سیستم های تبرید صنعتی و تولید مواد شیمیایی پایه دارد. در این مقاله به بررسی جامع آمونیاک از تعریف و عملکرد فنی آن گرفته تا کاربردهای صنعتی استانداردهای مرتبط چالش ها و فناوری های نوین خواهیم پرداخت.
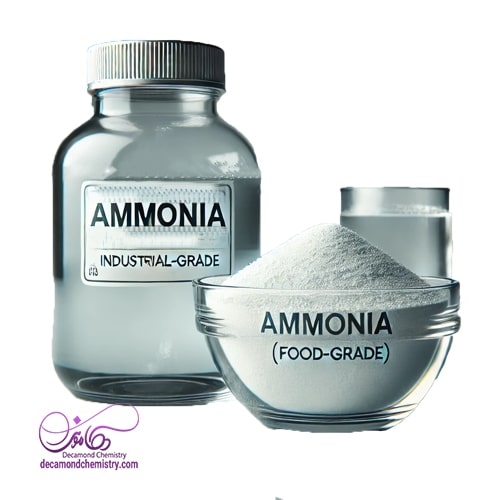
تعریف و عملکرد فنی آمونیاک
آمونیاک در شرایط استاندارد دما و فشار (STP) به صورت گاز وجود دارد اما به راحتی به مایع تبدیل می شود. این ترکیب مولکولی قطبی است که به دلیل وجود پیوندهای هیدروژنی نقطه جوش نسبتاً بالایی (-۳۳.۳۴ درجه سانتیگراد) نسبت به سایر هیدریدهای گروه نیتروژن دارد. از نظر شیمیایی آمونیاک یک باز ضعیف محسوب می شود و در واکنش با اسیدها نمک های آمونیوم را تشکیل می دهد.
عملکرد فنی آمونیاک در صنایع مختلف به خواص شیمیایی و فیزیکی آن وابسته است. به طور خلاصه می توان عملکردهای کلیدی آن را به شرح زیر دسته بندی کرد :
- منبع نیتروژن : آمونیاک منبع اصلی نیتروژن برای تولید کودهای شیمیایی نیتروژنی است. نیتروژن عنصری ضروری برای رشد گیاهان است و کودهای آمونیاکی نقش مهمی در افزایش بهره وری کشاورزی دارند.
- مبرد : آمونیاک به دلیل گرمای نهان تبخیر بالا و خواص ترمودینامیکی مطلوب یک مبرد کارآمد و سازگار با محیط زیست (در مقایسه با برخی مبردهای مصنوعی) در سیستم های تبرید صنعتی بزرگ محسوب می شود.
- ماده اولیه شیمیایی : آمونیاک ماده اولیه مهمی برای تولید طیف گسترده ای از مواد شیمیایی از جمله اسید نیتریک اوره نایلون مواد منفجره و داروها است.
- عامل تنظیم pH : آمونیاک محلول در آب (محلول آمونیاک یا آمونیوم هیدروکسید) به عنوان یک باز ضعیف برای تنظیم pH در فرآیندهای صنعتی و آزمایشگاهی کاربرد دارد.
- عامل احیا کننده : آمونیاک در برخی فرآیندهای صنعتی به عنوان عامل احیا کننده برای حذف اکسیدهای نیتروژن (NOx) از گازهای خروجی نیروگاه ها و خودروها استفاده می شود (فرایند SCR – Selective Catalytic Reduction).
اجزای اصلی و اصول کارکرد سیستم های تولید و استفاده از آمونیاک
تولید صنعتی آمونیاک عمدتاً از طریق فرایند هابر-بوش (Haber-Bosch process) انجام می شود. این فرایند که در اوایل قرن بیستم توسعه یافت انقلابی در تولید کودهای نیتروژنی ایجاد کرد و امکان تولید انبوه آمونیاک را فراهم ساخت.
فرایند هابر-بوش :
- تهیه گاز سنتز (Syngas) : در ابتدا گاز سنتز که مخلوطی از هیدروژن (H₂) و نیتروژن (N₂) است تهیه می شود. هیدروژن معمولاً از متان (گاز طبیعی) از طریق فرایند ریفرمینگ با بخار آب (Steam Reforming) به دست می آید. نیتروژن نیز از هوا جداسازی می شود.
- اصول کارکرد ریفرمینگ با بخار آب : در این فرایند متان (CH₄) در دمای بالا (حدود ۸۵۰ درجه سانتیگراد) و فشار بالا در حضور کاتالیزور نیکل با بخار آب واکنش می دهد و گاز سنتز (مخلوط CO و H₂) تولید می شود. واکنش به صورت زیر است :
- CH₄ + H₂O ⇌ CO + ۳H₂ (واکنش گرماگیر)
سپس گاز CO حاصل با بخار آب واکنش داده و هیدروژن بیشتری تولید می شود (واکنش شیفت گاز-آب – Water-Gas Shift Reaction) :
CO + H₂O ⇌ CO₂ + H₂ (واکنش گرمازا)
- خالص سازی گاز سنتز : گاز سنتز تولید شده حاوی ناخالصی هایی مانند CO₂ CO آرگون و متان است که باید قبل از ورود به راکتور سنتز آمونیاک حذف شوند. این خالص سازی معمولاً از طریق فرایندهای جذب جداسازی غشایی و یا شستشو انجام می شود.
- سنتز آمونیاک : گاز سنتز خالص شده وارد راکتور سنتز آمونیاک می شود. در این راکتور نیتروژن و هیدروژن در حضور کاتالیزور آهن (معمولاً آهن مغناطیسی – Fe₃O₄) در دمای بالا (۴۰۰-۵۰۰ درجه سانتیگراد) و فشار بالا (۱۵۰-۳۰۰ بار) با هم واکنش داده و آمونیاک تولید می کنند. واکنش سنتز آمونیاک به صورت زیر است :
- N₂ + ۳H₂ ⇌ ۲NH₃ (واکنش گرمازا)
این واکنش تعادلی است و به دلیل گرمازا بودن دماهای پایین تر تعادل را به سمت تولید آمونیاک بیشتر هدایت می کنند. اما به دلیل کند بودن سرعت واکنش در دماهای پایین دمای بهینه با در نظر گرفتن سرعت واکنش و تعادل شیمیایی انتخاب می شود. فشار بالا نیز به دلیل کاهش حجم در واکنش تعادل را به سمت تولید آمونیاک بیشتر سوق می دهد (اصل لوشاتلیه).
- جداسازی و خالص سازی آمونیاک : آمونیاک تولید شده از راکتور خارج شده و از مخلوط گازی جدا می شود. این جداسازی معمولاً از طریق چگالش (Condensation) انجام می شود. آمونیاک مایع در دماهای پایین چگالیده شده و از گازهای واکنش نداده (نیتروژن و هیدروژن) جدا می گردد. گازهای واکنش نداده دوباره به راکتور بازگردانده می شوند تا راندمان فرایند افزایش یابد.
سیستم های استفاده از آمونیاک :
سیستم های استفاده از آمونیاک بسته به کاربرد متفاوت هستند. به عنوان مثال در سیستم های تبرید آمونیاکی اجزای اصلی عبارتند از :
- کمپرسور : فشار مبرد آمونیاک را افزایش داده و آن را به گاز داغ و پرفشار تبدیل می کند.
- کندانسور : گاز آمونیاک پرفشار در کندانسور خنک شده و به مایع تبدیل می شود. گرما از مبرد به محیط اطراف منتقل می شود.
- شیر انبساط (Expansion Valve) : مایع آمونیاک پرفشار از شیر انبساط عبور کرده و فشار آن کاهش می یابد. این کاهش فشار باعث تبخیر بخشی از مایع و کاهش دمای آن می شود.
- اواپراتور : مبرد آمونیاک کم فشار و سرد وارد اواپراتور می شود. در اواپراتور آمونیاک تبخیر شده و گرمای محیط اطراف را جذب می کند. این فرایند باعث خنک شدن محیط می شود. گاز آمونیاک دوباره به کمپرسور بازگردانده می شود تا چرخه تبرید تکرار شود.
اصول کارکرد سیستم تبرید آمونیاکی بر پایه چرخه تبرید تراکمی (Vapor Compression Cycle) است. این چرخه بر اساس تغییر فاز مبرد (تبخیر و چگالش) و انتقال گرما در دماهای مختلف کار می کند. آمونیاک به دلیل خواص ترمودینامیکی مناسب به ویژه گرمای نهان تبخیر بالا مبرد بسیار کارآمدی در سیستم های تبرید صنعتی بزرگ است.
کاربردهای صنعتی و مثال هایی از صنایع مختلف
آمونیاک به دلیل خواص منحصر به فرد خود کاربردهای بسیار گسترده ای در صنایع مختلف دارد. برخی از مهم ترین کاربردهای صنعتی آمونیاک عبارتند از :
-
صنعت کشاورزی (تولید کودهای نیتروژنی) :
- بیشترین کاربرد آمونیاک در تولید کودهای نیتروژنی است. آمونیاک به صورت مستقیم (آمونیاک بی مایع) یا به صورت غیرمستقیم برای تولید کودهای مختلف مانند اوره (Urea) نیترات آمونیوم (Ammonium Nitrate) سولفات آمونیوم (Ammonium Sulfate) و فسفات های آمونیوم (Ammonium Phosphates) به کار می رود.
- کودهای نیتروژنی نقش اساسی در افزایش بهره وری کشاورزی و تامین غذای جمعیت رو به رشد جهان دارند. نیتروژن عنصری کلیدی برای رشد گیاهان است و کودهای آمونیاکی این عنصر را به شکل قابل جذب برای گیاهان فراهم می کنند.
- مثال : شرکت های بزرگ تولید کود شیمیایی مانند شرکت کود شیمیایی اوره لردگان و شرکت پتروشیمی کرمانشاه در ایران و شرکت هایی مانند Nutrien و Yara International در سطح بین المللی از آمونیاک به عنوان ماده اولیه اصلی برای تولید کودهای نیتروژنی استفاده می کنند.
-
صنعت تبرید و تهویه مطبوع :
- آمونیاک به عنوان مبرد R۷۱۷ شناخته می شود و به دلیل خواص ترمودینامیکی عالی راندمان بالا و سازگاری با محیط زیست (پتانسیل تخریب لایه ازون صفر – ODP=۰ و پتانسیل گرمایش جهانی بسیار پایین – GWP=۰) در سیستم های تبرید صنعتی بزرگ سردخانه ها صنایع غذایی (مانند صنایع لبنی کشتارگاه ها صنایع نوشیدنی) و سیستم های تهویه مطبوع صنعتی کاربرد گسترده ای دارد.
- در مقایسه با مبردهای مصنوعی (مانند CFCs HCFCs و HFCs) که مشکلات زیست محیطی دارند آمونیاک یک جایگزین پایدارتر و کارآمدتر محسوب می شود. با این حال سمیت و اشتعال پذیری آمونیاک نیازمند رعایت نکات ایمنی و طراحی مناسب سیستم های تبرید است.
- مثال : بسیاری از سردخانه های بزرگ صنعتی کارخانجات فرآوری مواد غذایی و تاسیسات پتروشیمی از سیستم های تبرید آمونیاکی استفاده می کنند. شرکت هایی مانند Johnson Controls و Emerson Climate Technologies سیستم های تبرید صنعتی مبتنی بر آمونیاک را طراحی و تولید می کنند.
-
صنعت شیمیایی :
- آمونیاک ماده اولیه مهمی برای تولید طیف وسیعی از مواد شیمیایی پایه و محصولات واسطه ای است. برخی از مهم ترین کاربردهای آمونیاک در صنعت شیمیایی عبارتند از :
- تولید اسید نیتریک (Nitric Acid) : اسید نیتریک ماده اولیه برای تولید کودهای نیتراته مواد منفجره (مانند TNT) نایلون پلی یورتان و بسیاری از مواد شیمیایی دیگر است. اسید نیتریک از طریق فرایند استوالد (Ostwald process) با اکسیداسیون کاتالیستی آمونیاک تولید می شود.
- تولید اوره (Urea) : اوره علاوه بر کاربرد به عنوان کود در تولید رزین های اوره-فرمالدهید پلاستیک ها چسب ها و مواد خوراکی دام نیز کاربرد دارد. اوره از واکنش آمونیاک با دی اکسید کربن در فشار و دمای بالا تولید می شود.
- تولید نایلون : آمونیاک در تولید کاپرولاکتام (Caprolactam) ماده اولیه برای تولید نایلون ۶ نقش دارد.
- تولید مواد منفجره : آمونیاک در تولید برخی مواد منفجره مانند نیترات آمونیوم و TNT به کار می رود.
- تولید مواد دارویی و بهداشتی : آمونیاک در تولید برخی داروها و مواد بهداشتی به عنوان ماده اولیه یا واسطه شیمیایی استفاده می شود.
- تولید مواد شوینده و پاک کننده : محلول آمونیاک (آمونیوم هیدروکسید) به عنوان یک باز ضعیف در برخی مواد شوینده و پاک کننده خانگی و صنعتی کاربرد دارد.
- مثال : شرکت های بزرگ پتروشیمی و صنایع شیمیایی مانند BASF Dow Chemical و SABIC از آمونیاک به عنوان ماده اولیه کلیدی در تولید محصولات شیمیایی خود استفاده می کنند. در ایران نیز شرکت های پتروشیمی مختلف از جمله پتروشیمی شیراز و پتروشیمی زاگرس در تولید اوره و سایر محصولات شیمیایی مبتنی بر آمونیاک فعال هستند.
- آمونیاک ماده اولیه مهمی برای تولید طیف وسیعی از مواد شیمیایی پایه و محصولات واسطه ای است. برخی از مهم ترین کاربردهای آمونیاک در صنعت شیمیایی عبارتند از :
-
صنعت معدن و متالورژی :
- آمونیاک در صنعت معدن و متالورژی در فرایندهای مختلفی از جمله استخراج فلزات تنظیم pH و رسوب دهی کاربرد دارد.
- مثال : در استخراج مس از کانی های اکسیدی آمونیاک برای لیچینگ (Leaching) و انحلال مس استفاده می شود. همچنین در فرایندهای تصفیه آب های معدنی و پساب های صنعتی آمونیاک برای تنظیم pH و رسوب دهی فلزات سنگین به کار می رود.
-
صنعت تصفیه آب و فاضلاب :
- آمونیاک در تصفیه آب آشامیدنی و فاضلاب به عنوان ضدعفونی کننده (در قالب کلرامین) و تنظیم کننده pH استفاده می شود.
- کلرامین ها از واکنش آمونیاک با کلر تولید می شوند و نسبت به کلر آزاد ماندگاری بیشتری در سیستم های توزیع آب دارند و بوی کمتری ایجاد می کنند.
- همچنین آمونیاک در فرایندهای حذف نیتروژن از فاضلاب (مانند فرایند نیتریفیکاسیون/دنیترریفیکاسیون) نقش دارد.
-
صنعت انرژی (کاربردهای نوظهور) :
- حامل هیدروژن : آمونیاک به عنوان یک حامل بالقوه برای هیدروژن مورد توجه قرار گرفته است. آمونیاک دارای چگالی هیدروژن بالایی است و حمل و نقل آن نسبت به هیدروژن خالص آسان تر است. آمونیاک می تواند در محل مصرف به هیدروژن و نیتروژن تجزیه شود (فرایند Cracking آمونیاک). هیدروژن حاصل می تواند در پیل های سوختی و سایر کاربردهای انرژی پاک استفاده شود.
- سوخت مستقیم : آمونیاک به عنوان یک سوخت مستقیم برای موتورهای احتراق داخلی و توربین های گازی نیز در حال بررسی است. احتراق آمونیاک اکسیدهای نیتروژن (NOx) تولید می کند که باید کنترل شوند اما در مقایسه با سوخت های فسیلی انتشار گازهای گلخانه ای کمتری دارد.
- ذخیره سازی انرژی : آمونیاک می تواند به عنوان یک ماده ذخیره ساز انرژی در سیستم های انرژی تجدیدپذیر (مانند انرژی خورشیدی و بادی) مورد استفاده قرار گیرد. انرژی مازاد تولید شده می تواند برای تولید آمونیاک از طریق فرایندهای الکترولیتی (آمونیاک سبز) استفاده شود و سپس آمونیاک ذخیره شده در زمان نیاز به انرژی تبدیل شود.
بررسی استانداردهای بین المللی و فناوری های پیشرفته مرتبط
استانداردهای بین المللی مرتبط با آمونیاک :
- ISO ۴۵۰۰۱ (سیستم مدیریت ایمنی و بهداشت شغلی) : این استاندارد بین المللی الزامات یک سیستم مدیریت ایمنی و بهداشت شغلی را مشخص می کند که برای مدیریت ریسک های ایمنی و بهداشتی مرتبط با کار و ایجاد محیط کار ایمن و سالم برای کارکنان ضروری است. در صنایع مرتبط با آمونیاک رعایت این استاندارد برای اطمینان از ایمنی کارکنان و محیط زیست بسیار مهم است.
- استانداردهای مربوط به طراحی و ساخت مخازن تحت فشار : برای ذخیره سازی و حمل و نقل آمونیاک مایع مخازن تحت فشار مطابق با استانداردهای معتبر بین المللی مانند ASME Boiler and Pressure Vessel Code و EN ۱۳۴۴۵ طراحی و ساخته می شوند. این استانداردها الزامات مربوط به مواد طراحی ساخت بازرسی و آزمایش مخازن تحت فشار را مشخص می کنند تا از ایمنی و عملکرد مطمئن آنها اطمینان حاصل شود.
- استانداردهای ایمنی و بهداشتی مربوط به حمل و نقل مواد خطرناک : حمل و نقل آمونیاک به عنوان یک ماده خطرناک تابع مقررات و استانداردهای بین المللی مانند ADR (توافقنامه اروپایی حمل و نقل بین المللی جاده ای کالاهای خطرناک) و IMDG Code (کد بین المللی دریایی کالاهای خطرناک) است. این استانداردها الزامات مربوط به بسته بندی برچسب زنی بارگیری تخلیه و حمل و نقل ایمن آمونیاک را تعیین می کنند.
- استانداردهای مربوط به سیستم های تبرید آمونیاکی : استانداردهایی مانند ASHRAE ۱۵ (ایمنی سیستم های تبرید) و EN ۳۷۸ (سیستم های تبرید و پمپ های حرارتی – ایمنی و الزامات زیست محیطی) الزامات ایمنی و زیست محیطی مربوط به طراحی نصب بهره برداری و نگهداری سیستم های تبرید آمونیاکی را مشخص می کنند. این استانداردها به منظور کاهش خطرات ناشی از سمیت و اشتعال پذیری آمونیاک و بهینه سازی عملکرد سیستم های تبرید تدوین شده اند.
- استانداردهای زیست محیطی مربوط به انتشار آمونیاک : استانداردهای زیست محیطی مختلفی در سطح ملی و بین المللی برای محدود کردن انتشار آمونیاک به هوا و آب وجود دارد. این استانداردها به منظور کاهش اثرات منفی آمونیاک بر محیط زیست و سلامت انسان تدوین شده اند. به عنوان مثال دستورالعمل های اتحادیه اروپا در مورد انتشار صنعتی (IED) و استانداردهای سازمان حفاظت محیط زیست ایالات متحده (EPA) محدودیت هایی را برای انتشار آمونیاک از صنایع مختلف تعیین کرده اند.
فناوری های پیشرفته مرتبط با آمونیاک :
- آمونیاک سبز (Green Ammonia) : تولید آمونیاک سبز با استفاده از هیدروژن تولید شده از منابع تجدیدپذیر (مانند الکترولیز آب با استفاده از انرژی خورشیدی یا بادی) و نیتروژن جداسازی شده از هوا یک فناوری نوظهور و پایدار برای تولید آمونیاک است. آمونیاک سبز می تواند نقش مهمی در کاهش انتشار گازهای گلخانه ای ناشی از تولید آمونیاک سنتی و توسعه اقتصاد هیدروژنی ایفا کند.
- فرایندهای نوین سنتز آمونیاک : تحقیقات گسترده ای برای توسعه فرایندهای نوین سنتز آمونیاک با راندمان بالاتر مصرف انرژی کمتر و انتشار کربن پایین تر در حال انجام است. این فرایندها شامل استفاده از کاتالیزورهای پیشرفته تر فرایندهای الکتروشیمیایی سنتز آمونیاک در دما و فشار پایین تر و فرایندهای بیولوژیکی سنتز آمونیاک با استفاده از میکروارگانیسم ها است.
- سیستم های تبرید آمونیاک-CO₂ Cascade : سیستم های تبرید cascade که از ترکیب آمونیاک و دی اکسید کربن (CO₂) به عنوان مبرد استفاده می کنند به دلیل راندمان بالا و کاهش بار آمونیاک در سیستم مورد توجه قرار گرفته اند. در این سیستم ها آمونیاک در سیکل دمای بالا و CO₂ در سیکل دمای پایین استفاده می شود.
- فناوری های بازیابی و بازیافت آمونیاک : فناوری های پیشرفته ای برای بازیابی و بازیافت آمونیاک از جریان های پسماند صنعتی و کشاورزی در حال توسعه است. این فناوری ها می توانند به کاهش ضایعات آمونیاک حفاظت از محیط زیست و بهبود پایداری فرایندهای صنعتی کمک کنند.
- کاربرد نانومواد در کاتالیزورهای سنتز آمونیاک : استفاده از نانومواد به عنوان کاتالیزور در فرایند هابر-بوش می تواند باعث افزایش فعالیت کاتالیزوری بهبود راندمان و کاهش مصرف انرژی در تولید آمونیاک شود. تحقیقات در این زمینه بر توسعه نانوکاتالیزورهای آهن روتنیم و سایر فلزات متمرکز است.
چالش ها و محدودیت های فنی
با وجود کاربردهای گسترده و مزایای متعدد آمونیاک چالش ها و محدودیت های فنی نیز در استفاده از آن وجود دارد :
- سمیت و خطرات ایمنی : آمونیاک گازی سمی و خورنده است و در غلظت های بالا می تواند برای انسان و محیط زیست خطرناک باشد. استنشاق غلظت های بالای آمونیاک می تواند باعث تحریک شدید مجاری تنفسی سوختگی ریه و حتی مرگ شود. تماس آمونیاک مایع با پوست و چشم نیز می تواند باعث سوختگی شدید شود. همچنین آمونیاک در غلظت های بالا قابل اشتعال است و می تواند مخلوط های انفجاری با هوا تشکیل دهد. به همین دلیل رعایت نکات ایمنی و طراحی مناسب سیستم های استفاده از آمونیاک برای جلوگیری از حوادث و حفاظت از سلامت انسان و محیط زیست بسیار ضروری است.
- خورندگی : آمونیاک خورنده است و می تواند با برخی مواد مانند مس روی و برنج واکنش داده و باعث خوردگی آنها شود. به همین دلیل در سیستم های استفاده از آمونیاک باید از مواد مقاوم در برابر خوردگی مانند فولاد کربنی فولاد ضد زنگ و آلومینیوم استفاده شود.
- مصرف انرژی بالای فرایند هابر-بوش : فرایند هابر-بوش که فرایند اصلی تولید آمونیاک است فرایندی انرژی بر است و نیاز به دما و فشار بالا دارد. تولید هیدروژن مورد نیاز برای فرایند هابر-بوش نیز معمولاً از گاز طبیعی انجام می شود که منجر به انتشار گازهای گلخانه ای می شود. این موضوع نگرانی های زیست محیطی را در مورد تولید آمونیاک سنتی افزایش داده است و ضرورت توسعه فرایندهای تولید آمونیاک پایدارتر و کم کربن را برجسته می کند.
- مشکلات حمل و نقل و ذخیره سازی : حمل و نقل و ذخیره سازی آمونیاک به دلیل سمی و خطرناک بودن آن نیازمند رعایت مقررات و استانداردهای ایمنی سختگیرانه و استفاده از تجهیزات و مخازن مخصوص است. حمل و نقل آمونیاک معمولاً به صورت مایع تحت فشار و در دماهای پایین انجام می شود که نیازمند زیرساخت های خاص است.
- بوی زننده : آمونیاک بوی بسیار تند و زننده ای دارد که می تواند برای افراد آزاردهنده باشد و در صورت نشت آمونیاک به سرعت قابل تشخیص است. اگرچه این بو به عنوان یک هشدار طبیعی عمل می کند اما می تواند در محیط های صنعتی و کشاورزی که با آمونیاک سروکار دارند مشکل ساز باشد.
نکات کلیدی برای بهینه سازی و بهبود عملکرد
برای بهینه سازی و بهبود عملکرد سیستم های تولید و استفاده از آمونیاک می توان به نکات کلیدی زیر توجه کرد :
- بهینه سازی فرایند هابر-بوش :
- بهبود کاتالیزورها : توسعه کاتالیزورهای جدید با فعالیت و گزینش پذیری بالاتر می تواند باعث افزایش راندمان فرایند و کاهش مصرف انرژی شود. نانوکاتالیزورها و کاتالیزورهای مبتنی بر فلزات غیر گرانبها از جمله زمینه های تحقیقاتی فعال در این زمینه هستند.
- بهینه سازی شرایط عملیاتی : تنظیم دقیق دما فشار و نسبت واکنش دهنده ها در راکتور سنتز آمونیاک می تواند باعث بهبود راندمان و کاهش مصرف انرژی شود. استفاده از مدل سازی و شبیه سازی فرایند برای تعیین شرایط بهینه عملیاتی می تواند مفید باشد.
- بازیابی و بازچرخانی انرژی : بازیابی گرمای واکنش گرمازای سنتز آمونیاک و استفاده از آن برای پیش گرم کردن مواد اولیه یا تولید بخار می تواند باعث افزایش راندمان انرژی فرایند شود. همچنین بازچرخانی گازهای واکنش نداده به راکتور راندمان کلی فرایند را بهبود می بخشد.
- افزایش ایمنی سیستم ها :
- طراحی سیستم های ایمن : طراحی سیستم های استفاده از آمونیاک باید با رعایت کامل استانداردهای ایمنی و با در نظر گرفتن خطرات احتمالی انجام شود. استفاده از سیستم های تشخیص نشت آمونیاک سیستم های تهویه مناسب و سیستم های اطفاء حریق از جمله اقدامات ضروری برای افزایش ایمنی سیستم ها هستند.
- آموزش و تربیت پرسنل : آموزش و تربیت پرسنل در زمینه handling ایمن آمونیاک روش های واکنش در شرایط اضطراری و استفاده از تجهیزات ایمنی نقش مهمی در پیشگیری از حوادث دارد.
- پایش و بازرسی دوره ای : پایش و بازرسی دوره ای تجهیزات و سیستم های مرتبط با آمونیاک می تواند به شناسایی و رفع مشکلات احتمالی قبل از وقوع حادثه کمک کند.
- کاهش اثرات زیست محیطی :
- توسعه آمونیاک سبز : استفاده از منابع تجدیدپذیر انرژی برای تولید هیدروژن و سنتز آمونیاک سبز می تواند به کاهش انتشار گازهای گلخانه ای ناشی از تولید آمونیاک کمک کند.
- کاهش انتشار آمونیاک : استفاده از فناوری های پیشرفته برای کاهش انتشار آمونیاک به هوا و آب مانند سیستم های scrubbers سیستم های تصفیه پساب و روش های کشاورزی دقیق که مصرف کود را بهینه می کنند ضروری است.
- بازیابی و بازیافت آمونیاک : توسعه و استفاده از فناوری های بازیابی و بازیافت آمونیاک از جریان های پسماند صنعتی و کشاورزی می تواند به کاهش ضایعات آمونیاک و حفاظت از محیط زیست کمک کند.
- بهبود راندمان سیستم های تبرید آمونیاکی :
- بهینه سازی طراحی سیستم : طراحی بهینه سیستم های تبرید آمونیاکی با توجه به نوع کاربرد و شرایط عملیاتی می تواند باعث افزایش راندمان و کاهش مصرف انرژی شود.
- استفاده از کمپرسورهای با راندمان بالا : استفاده از کمپرسورهای مدرن با راندمان بالا و کنترل سرعت متغیر می تواند مصرف انرژی سیستم های تبرید آمونیاکی را کاهش دهد.
- نگهداری و سرویس دوره ای : نگهداری و سرویس دوره ای سیستم های تبرید آمونیاکی شامل بررسی و تنظیم پارامترهای سیستم تمیزکاری کندانسور و اواپراتور و اطمینان از عملکرد صحیح اجزا می تواند راندمان سیستم را حفظ و طول عمر آن را افزایش دهد.
نتیجه گیری علمی و تخصصی
آمونیاک به عنوان یک ترکیب شیمیایی حیاتی نقش بسیار مهمی در صنایع مختلف به ویژه در کشاورزی تبرید و صنعت شیمیایی ایفا می کند. فرایند هابر-بوش اگرچه دستاوردی بزرگ در تولید آمونیاک بوده است اما فرایندی انرژی بر و دارای اثرات زیست محیطی است. توسعه فناوری های نوین مانند تولید آمونیاک سبز فرایندهای سنتز آمونیاک با راندمان بالاتر و سیستم های تبرید آمونیاک-CO₂ cascade به منظور افزایش پایداری و کاهش اثرات منفی آمونیاک بر محیط زیست ضروری است.
با توجه به چالش ها و محدودیت های فنی آمونیاک رعایت دقیق استانداردهای ایمنی بهینه سازی فرایندهای تولید و استفاده و توسعه فناوری های پیشرفته برای بهره برداری ایمن کارآمد و پایدار از این ماده شیمیایی ارزشمند از اهمیت بالایی برخوردار است. تحقیقات و نوآوری های مستمر در زمینه آمونیاک نقش کلیدی در تضمین نقش آن به عنوان یک ماده شیمیایی کلیدی در آینده صنایع مختلف خواهد داشت.
پرسش و پاسخ
۱. آمونیاک چه خطراتی دارد و چگونه می توان از آنها پیشگیری کرد؟
آمونیاک گازی سمی خورنده و قابل اشتعال است. خطرات اصلی آمونیاک شامل سمیت تنفسی سوختگی پوست و چشم و خطر انفجار در غلظت های بالا است. برای پیشگیری از این خطرات رعایت نکات ایمنی زیر ضروری است :
- استفاده از تجهیزات حفاظت فردی (PPE) : هنگام کار با آمونیاک استفاده از تجهیزات حفاظت فردی مناسب مانند ماسک تنفسی عینک ایمنی دستکش های مقاوم در برابر مواد شیمیایی و لباس محافظ ضروری است.
- تهویه مناسب : محیط های کاری که در آنها با آمونیاک سروکار دارند باید دارای تهویه مناسب باشند تا از تجمع گاز آمونیاک جلوگیری شود.
- سیستم های تشخیص نشت آمونیاک : نصب سیستم های تشخیص نشت آمونیاک در محل های نگهداری و استفاده از آمونیاک می تواند به تشخیص سریع نشت و انجام اقدامات لازم برای جلوگیری از حوادث کمک کند.
- آموزش و تربیت پرسنل : آموزش و تربیت پرسنل در زمینه خطرات آمونیاک روش های handling ایمن و اقدامات اضطراری در صورت نشت آمونیاک بسیار مهم است.
- نگهداری و بازرسی دوره ای تجهیزات : نگهداری و بازرسی دوره ای تجهیزات و سیستم های مرتبط با آمونیاک می تواند به شناسایی و رفع مشکلات احتمالی و اطمینان از عملکرد ایمن آنها کمک کند.
۲. آمونیاک سبز چیست و چه اهمیتی دارد؟
آمونیاک سبز به آمونیاکی اطلاق می شود که با استفاده از فرایندهای پایدار و کم کربن تولید شده باشد. در روش سنتی تولید آمونیاک (فرایند هابر-بوش) هیدروژن مورد نیاز از گاز طبیعی (یک سوخت فسیلی) به دست می آید که منجر به انتشار قابل توجه گازهای گلخانه ای می شود. آمونیاک سبز با استفاده از هیدروژن تولید شده از منابع تجدیدپذیر (مانند الکترولیز آب با استفاده از انرژی خورشیدی یا بادی) تولید می شود.
اهمیت آمونیاک سبز در موارد زیر است :
- کاهش انتشار گازهای گلخانه ای : تولید آمونیاک سبز می تواند به کاهش قابل توجه انتشار گازهای گلخانه ای ناشی از تولید آمونیاک سنتی کمک کند و به تحقق اهداف توافق نامه پاریس در زمینه تغییرات آب و هوایی کمک کند.
- توسعه اقتصاد هیدروژنی : آمونیاک سبز می تواند نقش مهمی در توسعه اقتصاد هیدروژنی ایفا کند. آمونیاک می تواند به عنوان یک حامل کارآمد برای هیدروژن عمل کند و امکان حمل و نقل و ذخیره سازی هیدروژن را به صورت ایمن و اقتصادی فراهم کند.
- تامین کود پایدار : استفاده از آمونیاک سبز در تولید کودهای نیتروژنی می تواند به تولید کودهای پایدارتر و سازگارتر با محیط زیست منجر شود و به توسعه کشاورزی پایدار کمک کند.
۳. آیا آمونیاک می تواند جایگزین سوخت های فسیلی شود؟
آمونیاک به عنوان یک سوخت جایگزین بالقوه برای سوخت های فسیلی به ویژه در بخش حمل و نقل و تولید برق مورد توجه قرار گرفته است. آمونیاک دارای مزایای زیر به عنوان سوخت است :
- عدم انتشار کربن : احتراق آمونیاک دی اکسید کربن تولید نمی کند و در نتیجه به کاهش انتشار گازهای گلخانه ای کمک می کند.
- چگالی انرژی بالا : آمونیاک چگالی انرژی حجمی بالاتری نسبت به هیدروژن دارد و حمل و نقل و ذخیره سازی آن آسان تر است.
- زیرساخت های موجود : زیرساخت های موجود برای تولید حمل و نقل و ذخیره سازی آمونیاک تا حدی قابل استفاده برای استفاده از آمونیاک به عنوان سوخت هستند.
با این حال چالش هایی نیز در استفاده از آمونیاک به عنوان سوخت وجود دارد :
- انتشار اکسیدهای نیتروژن (NOx) : احتراق آمونیاک اکسیدهای نیتروژن (NOx) تولید می کند که آلاینده های هوا هستند و باید کنترل شوند.
- سمیت و بوی زننده : آمونیاک گازی سمی و دارای بوی زننده است که نیازمند رعایت نکات ایمنی در استفاده به عنوان سوخت است.
- نیاز به فناوری های احتراق مناسب : برای احتراق کارآمد و کم آلاینده آمونیاک نیاز به توسعه فناوری های احتراق مناسب مانند موتورهای احتراق داخلی و توربین های گازی سازگار با آمونیاک است.
با وجود چالش ها تحقیقات و توسعه فناوری ها در زمینه استفاده از آمونیاک به عنوان سوخت در حال پیشرفت است و پتانسیل آمونیاک برای ایفای نقش مهم در گذار به انرژی پاک و کاهش وابستگی به سوخت های فسیلی قابل توجه است.
این همه تعریف از مزایای آمونیاک کردید ولی کسی از بوی وحشتناکش چیزی نگفت! یه بار نزدیک یه کارخونه کودسازی رد شدم تا چند ساعت سردرد داشتم. این بو واقعا قابل تحمل نیست.
تو مقاله نوشتید مبرد خوبیه ولی من شنیدم خیلی خطرناکه و نشت کنه فاجعه به بار میاد. سیستم های تبرید آمونیاکی واقعا ایمن هستن؟
برای کشاورزی واقعا کودهای آمونیاکی اینقدر تاثیر دارن؟ من کود شیمیایی دیگه استفاده می کنم ارزش داره کود آمونیاکی رو امتحان کنم؟
مقاله خوبی بود ولی خیلی تخصصی بود. برای یه آدم عادی که هیچی از شیمی نمیدونه یکم سنگین بود. میشد ساده تر توضیح بدید.
تولید آمونیاک سبز رو گفتید ولی اصلا توضیح ندادید چطوریه. میشه بیشتر در مورد فرایند تولیدش توضیح بدید؟
من تو یه کارخونه کار می کنم که از آمونیاک استفاده می کنن. ایمنی خیلی مهمه ولی خیلی جاها رعایت نمیشه. مقاله شما خوبه ولی کاش بیشتر روی نکات ایمنی تاکید می کردید.
من یه سردخونه کوچیک دارم. به نظرتون سیستم تبرید آمونیاکی به درد من میخوره یا نه؟ هزینه اش چقدره؟
این همه کاربرد داره آمونیاک ولی باز میگن خطرناکه! بالاخره خوبه یا بد؟ آدم گیج میشه!
تو مقاله گفتید آمونیاک خورنده است. پس چطوری تو صنعت استفاده میشه؟ مگه به دستگاه ها آسیب نمیزنه؟
مقاله خیلی کامل بود دستتون درد نکنه. فقط یه سوال این فرایند هابر-بوش که گفتید خیلی قدیمیه هنوز هم بهترین روشه؟ روش جدیدتری نیست؟
من شنیدم آمونیاک رو به عنوان سوخت هم استفاده می کنن. این درسته؟ چطوری میشه ازش به عنوان سوخت استفاده کرد؟
مقاله خوبیه ولی خیلی جانبدارانه نوشته شده. از چالش ها و محدودیت ها هم گفتید ولی بازم انگار فقط مزایا رو دیدید.
من تو یه مزرعه کار می کنم و با کودهای آمونیاکی سروکار دارم. همیشه نگران خطراتش هستم. مقاله شما یکم خیالمو راحت کرد ولی بازم ترس دارم.
این آمونیاک سبز که میگید خیلی خوبه ولی کی قراره واقعا تجاری بشه؟ الان فقط حرفه یا واقعا عملی شده؟
چرا اسم آمونیاک اینقدر عجیب غریبه؟ ریشه اسمش چیه؟
من برای تصفیه آب استخر دنبال یه ماده ضدعفونی کننده می گردم. آمونیاک به درد من میخوره؟
مقاله تخصصی بود ولی خوندنش سخت نبود. اطلاعات خوبی داشت. ممنون از نویسنده.
این فرایند بازیافت آمونیاک که گفتید خیلی جالبه. میشه بیشتر در مورد این فناوری ها توضیح بدید؟
من شنیدم آمونیاک برای محیط زیست ضرر داره. این درسته؟ اگه ضرر داره چرا انقدر استفاده میشه؟
مقاله خوبی بود ولی کاش مثال های صنعتی بیشتری میزدید. فقط اسم شرکت ها رو گفتید کافی نیست.